Crane Stability: Creating Stable Working Platforms for Mobile and Crawler Cranes
Date: May 01, 2025
Mobile cranes are essential plant items for infrastructure and building projects. Crane stability on site must be properly considered to ensure safe operations. Despite this, every year sees a number of mobile cranes toppling over, with high risk of personal injury and damage to property. What are the causes and how can crane stability on site be ensured.
In this article, we will be discussing the steps needed for ensuring crane stability on-site along with the guidance for the safe use of cranes:
- Common causes of crane accidents
- BS 7121-2-3: 2012 - Code of practice for the safe use of mobile cranes
- Crane Stability on site - risks and responsibilities
- Working Platforms for safe operation of mobile cranes on site
- What is a working platform certificate?
- Assessing ground conditions for crane operation<
- Hazardous ground conditions
- Crane ground bearing pressure formula
- Design ground stabilised crane platforms with Tensar+
The topic of working platform design for crane stability on site is dealt with in greater depth below.
Common causes of crane accidents
There are multiple hazards when operating mobile cranes on site. Each must be considered and managed. We can consider these in three categories. Mechanical equipment, method of working, and foundations.
Mechanical equipment issues
- Poorly designed or manufactured
- Inadequate routine maintenance
Method of working
- Inexperienced operators
- Inadequate supervision
- Incorrect crane capacity
- Lifting excessive load
- Poor planning of the lift operation
- Operating in excessive winds
Foundations
- Inadequate or incorrect ground assessment
- The presence of unidentified subsurface voids
- Inadequately designed outrigger foundation
- Inadequate working platform design
- Poorly constructed working platform
BS 7121-2-3:2012 - Code of practice for the safe use of mobile cranes
The British Standards BS 7121-2-3 Code of Practice for the safe use of cranes - Inspection, maintenance and thorough examination - mobile cranes, is part of the BS7121 series of British Standards that deal with the safe use cranes. It provides recommendations for pre-use checks, maintenance, and testing of mobile cranes, including wheeled cranes, truck-mounted cranes, and crawler-mounted cranes, all commonly used on construction sites. The Code is intended to protect the safety of crane operators and others involved in lifting operations. The Code does not cover the design of foundations and working platforms for the safe operation of mobile cranes. Tensar can assist with the economic design of working platforms for mobile cranes.
Crane Stability on Site – Risks and Responsibilities
Cranes for use on construction sites are usually owned and operated by specialist companies. A construction company requiring the use of a crane on a project can procure this in one of two ways. The crane can be hired with its operator, or as a contract lift. In all cases the construction company should ensure that a competent person has planned the lift and that a safe system of work is followed. In addition, they must be satisfied that the crane is properly inspected and maintained and safe to travel on roads to the site.
When the crane is hired, the hirer is responsible for all aspects of the lifting operation. They must ensure there is a safe lifting plan in place complying with BS 7121-2-3 and based on adequate load information. Also, that they provide a competent operator, and that all operations are properly supervised and carried out safely. The crane supplier must provide technical information such as lift capacity and outrigger loads. The supplier must also satisfy themselves that a safe lifting plan is in place.
When a contract lift service is used, the crane supplier will carry out the lift. They are responsible for lift planning and supervision and for ensuring adequate stability of the crane. The employing organization, the construction company, must provide information on ground bearing capacity and details of the load to be lifted.
In all cases, the construction company is responsible for providing a foundation or working platform that has adequate bearing capacity for safe operation of the crane. It is now more common for the construction company to be asked for working platforms to be certified for this purpose by a competent engineer.
Windpark Bommelewaard, Netherlands - Crane pad constructed on a 1,2 m mechanically stabilised layer with three layers of Tensar Geogrid
Working Platforms for safe operation of mobile cranes on site
To enable the safe operation and stability of mobile cranes on site, the surface on which they travel and operate must have sufficient strength to carry the applied loading without excessive settlement. Where the existing ground does not have adequate bearing capacity, a working platform can be constructed to support the crane and distribute the loads over the ground beneath.
Working platforms are typically constructed by compacting a layer of unbound granular fill directly over the existing ground. The thicker the platform, the greater the load distribution. Weak or variable ground conditions can require working platforms over one metre thick. A more economic option is to design the platform as a mechanically stabilised layer incorporating one or more layers of Tensar geogrid. This will result in a thinner working platform that delivers the same load distribution as a thicker platform, saving on expensive imported fill and construction time.
Working platforms stabilised by Tensar geogrid
What is a working platform certificate?
Crane suppliers may insist on a working platform certificate to confirm that the platform has been properly designed and constructed and will be adequately maintained. The main contractor will be required to sign the certificate, which will then be made available to the person planning the lift operation. The Federation of Piling Specialists (FPS) provides useful guidance and a template certificate for working platforms for tracked plant. Tensar can provide a working platform design that is accepted for certification purposes.
Assessing ground conditions for crane operation
It is essential that a geotechnical survey of the full site area intended for crane movement and operation is completed in advance of working platform design. A ground investigation report will be prepared and the results interpreted by a qualified geotechnical engineer. The maximum permissible ground bearing pressure across the site will be identified and when required, assessments of potential settlement under sustained loading. Hazards or ground irregularities will be identified and reported to the engineer responsible for working platform design.
Tensar's Engineers can support you on your next working platform project
Request a free feasibility assessment or share your project requirements and our team will be in touch.
Request feasibility assesment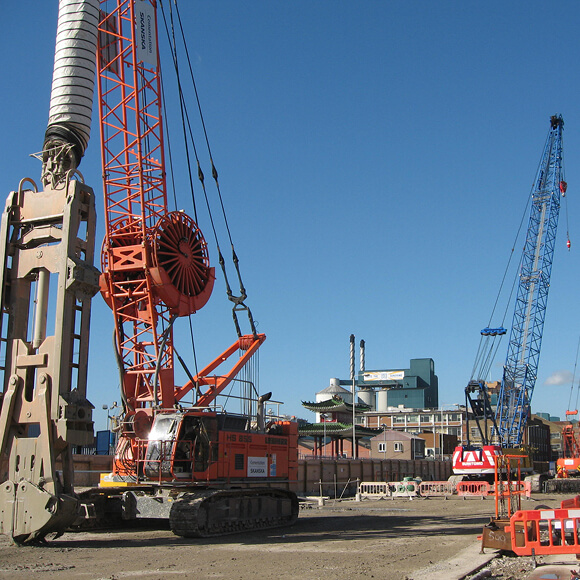
Hazardous ground conditions
The ground investigation and geotechnical report will identify any ground related hazards or irregularities that might influence crane stability and design of the working platform.
Uncompacted fill
On sites where there are areas of fill material, it is possible that some areas have received minimal compaction. This is common on brownfield sites where there may also be buried services and structures that could collapse under load.
Nearby buried structures that have weakened the surrounding ground
Locations adjacent to buried structures may have poorly compacted backfill. This could settle under load and needs to be investigated.
Trenches and embankments
The working platform design will need to take account of the proximity of open excavations or adjacent steeply sloping ground. The ground could collapse into the excavation under the applied loading.
Weather conditions
The ground bearing capacity is related to soil moisture content. Increased water content reduces soil strength. Earthworks operations on a site can divert surface water onto the parts of the site previously well drained, changing the soil strength. This must be avoided by ensuring proper drainage and stormwater control measures are in place.
Underground utility pipelines
Buried services and pipelines present a hazard. The pipe may collapse or the backfill may be poorly compacted. Pre-existing services and pipelines must be identified and, if possible, working over them avoided.
Crane ground bearing pressure calculation
The calculation of crane ground pressures applied during transportation and operation of a crane is complex and must be carried out by a competent person.
The stability of a crane is dependent on the bearing capacity of the working platform below the tracks or outrigger mats. The designer of the working platform will need to know the crane ground bearing pressures that will be applied during different stages of the operation.
Calculations of the crane loads on the outriggers or tracks need to consider the following.
- The weight and configuration of the crane
- The weight of rigging gear
- The lift load
- Dynamic loading due to wind pressure and operation
- The lift operation load cases
Load Cases
During lifting operations, the boom length, boom position, and slew angle will vary. This changes the forces on the outriggers or distribution of load beneath tracks. At the extreme, almost the entire load may be applied to one outrigger or one track. The load cases without lift load must also be considered as the counterweight load is considerable.
Loads must be calculated for a series of load cases, to identify the worst load case from all configurations, with and without lift load.
Crane Mats
Wheeled mobile cranes use outriggers to increase stability. The bearing pressure below outriggers can be reduced by the use of crane mats. These will be metal, plastic or wooden mats, strong enough and stiff enough to distribute outrigger loads over a wider area. The calculated ground pressure below the crane mat will be used for the working platform design. Alternatively, the required crane mat size may be calculated based on a maximum permissible ground bearing pressure with appropriate factor of safety (FOS) applied.
The crane ground bearing pressure formula is as follows:
Crane outriggers
Design geogrid stabilised crane platforms with Tensar+
Working platform design is critical to ensure mobile crane stability and safe operation on site. Tensar+ software enables engineers to design working platforms for both wheeled mobile cranes with outriggers and tracked crawler cranes.
Alternatively, The design team at Tensar can provide a complete design service for certification purposes . The information required for the design will include
- Subgrade strength – A site investigation and geotechnical report are required to determine the subgrade condition and strength across the site.
- Fill material – The fill properties are needed. The granular fill should be durable, well graded and meet the drainage requirements
- Loading schedule – Information is needed on crane loading during transportation and for each critical load case during operation
Tensar design method for working platforms for mobile cranes
Traditionally, the calculation methods for working platforms have been quite empirical, using imprecise input parameters or involving the use of multiple design charts. These have tended to result in an overly conservative working platform thickness. Construction companies needed improved design methods that would avoid higher than necessary costs.
In response, Tensar developed a design method for working platforms that addresses all of these concerns. This is the T-Value method. T-value represents the load transfer efficiency of a granular layer.
Importantly, the T-value method enables the designer to correctly use an improved load transfer efficiency for a granular layer incorporating a stabilisation geogrid. This typically results in significant reductions in working platform thickness, with the cost-saving and environmental benefits that delivers.
For an explanation of working platform design and the Tensar design method, take a look at our video on how to use the T-value method.
Check out Andrew Lees in our Ground Coffee archives! In this episode, Andrew explains working platform design and the Tensar T-Value method.
Free online software to design your working platform
The Tensar+ platforms module allows you to model project specific conditions to calculate what a Tensar mechanically stabilised working platform will look like using the T-Value method.
Sign up here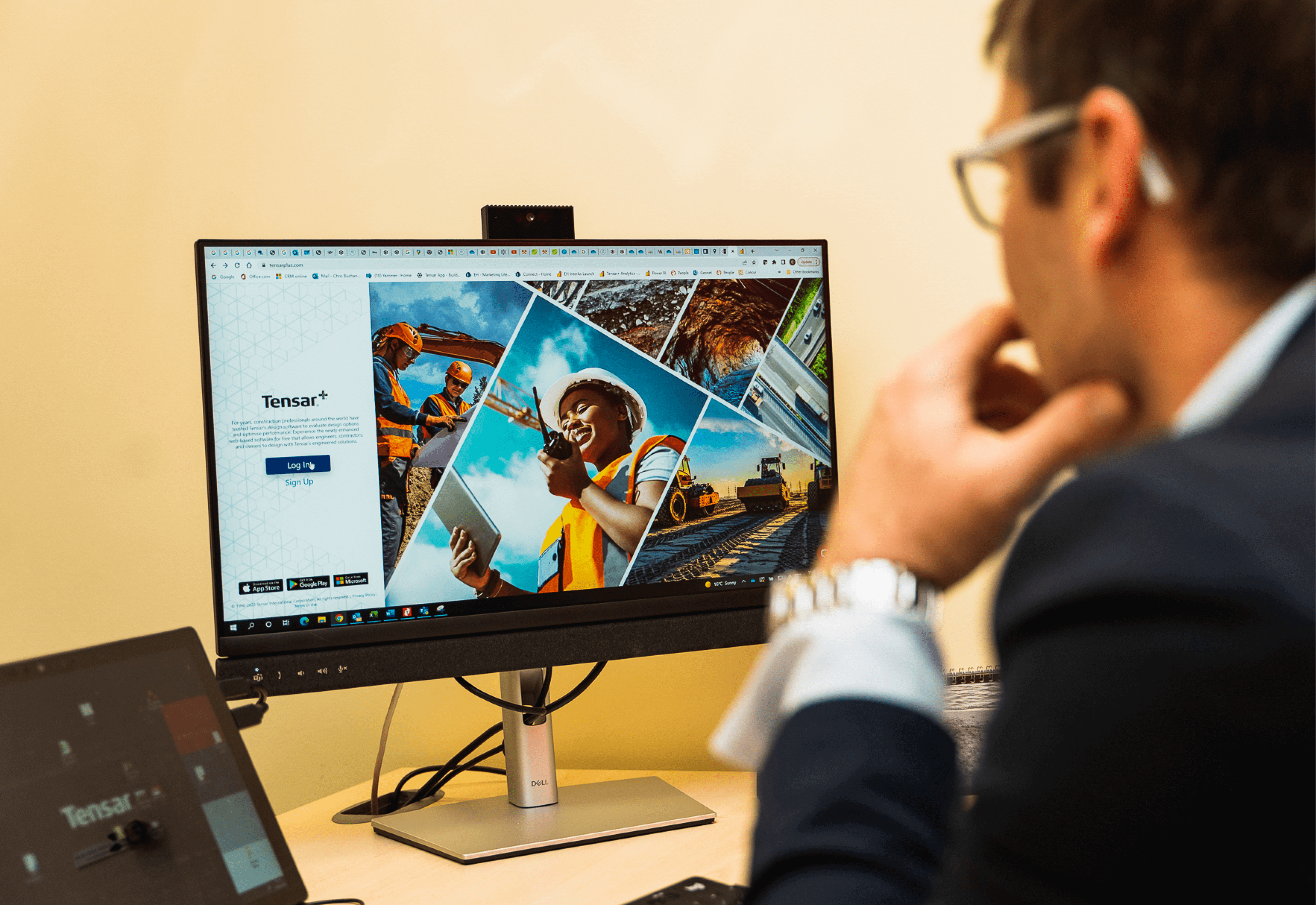
References
- Lees, A.S. (2020) The bearing capacity of a granular layer on clay. Proceedings of the Institution of Civil engineers – Geotechnical Engineering, 173, No. 3, 448-452
- Lees, A. S. and Abid, A (2023) The surface bearing capacity of a strong granular layer on weaker sand. Proceedings of the Institution of Civil Engineers – Geotechnical Engineering, https://doi.org/10.1680/jgeen.22.00094
- Lees, A.S. and Clausen, J; (2019). The strength envelope of granular soil stabilised by multi-axial geogrid in large triaxial tests. Canadian Geotechnical Journal https://doi.org/10.1139/cgj-2019-0036
- Lees, A.S. and Matthias, P. (2019) Bearing capacity of a geogrid-stabilised granular layer on clay. Ground Engineering Nov.2019, 28-33[TO6]